From the intricate patterns of the Meranaw’s langkit down to the extravagant banigs of the Tagolwanen, the art of weaving is just as integrally stitched into our Filipino identity as the craft itself.
Go down to any tourism office, any souvenir shop – from the high luxuries of Kultura Filipino down to small-time local kiosks during festivals – no “authentic Filipino experience” is complete without a woven little pasalubong for both yourself and your loved ones.
This is exactly why it’s more than a little disheartening when something so celebrated not only goes unappreciated, but undervalued.
Around 34 years ago, Hiroshi Ikeda, a Japanese agriculturist came to the village of Diwan, Dipolog City with the Organization for Industrial, Spiritual, and Cultural Advancement (OISCA) for a tree planting outreach program. While there, he noticed that their trees were crawling with nito vines and saw the opportunity to open a training center to teach locals about its uses.
While most of the men in the area were farmers, their wives didn’t have a source of income and decided to join the workshop where they were taught not just the skill of weaving, but how to prepare the vine for the process.
Now, half-subanen women residing in Sitio Pamansalan in the village make their living weaving hats, place mats, bags, and wallets from the very same vines they once dismissed as weeds.
They start the process by getting rid of the nodes with a knife before proceeding to break the vine into three strands by running it through with their nails. Afterwards, they leave them out to dry in the sun for no longer than 2 hours lest they run the risk of the vines growing too brittle and ultimately unusable.
The weaving process itself can take between 2 hours and 6 weeks depending on the product they’re making.

In terms of orders, they receive orders in bulk and assign one weaver to each item. If they were to receive an order of 50 bags, mats, and wallets, one weaver would make all the bags, another one would make the mats, and another one would be in charge of the wallets. Once finished, they would deliver their products to Dipolog City proper to meet with the buyer.
While they do operate on a preorder basis, they don’t have any ready-made products on display. So if you were to visit their village today, you wouldn’t be able to buy or even see their products, and because they are relatively unknown compared to other actual organizations and cooperatives, they receive minimal income. On record, largest income they have gotten from weaving is to be around only Php. 1,500.00.
According to Mrs. Lillian Bacang, one of the weavers, there used to be 15 of them in their community but because of the changing times, almost half of her fellow weavers left to pursue other opportunities and leaving only 8 of them to continue the business. However, despite them all being in good terms, they have yet to form a cooperative for themselves.
When they first started weaving, there was no shortage on supplies since, again, most people simply dismissed nito vines as weeds with no real use but as the years have gone by and they’ve made more and more products, supplies are starting to dwindle down.
In the end, some of them have to buy from sellers in other sitios instead of harvesting the vines themselves.
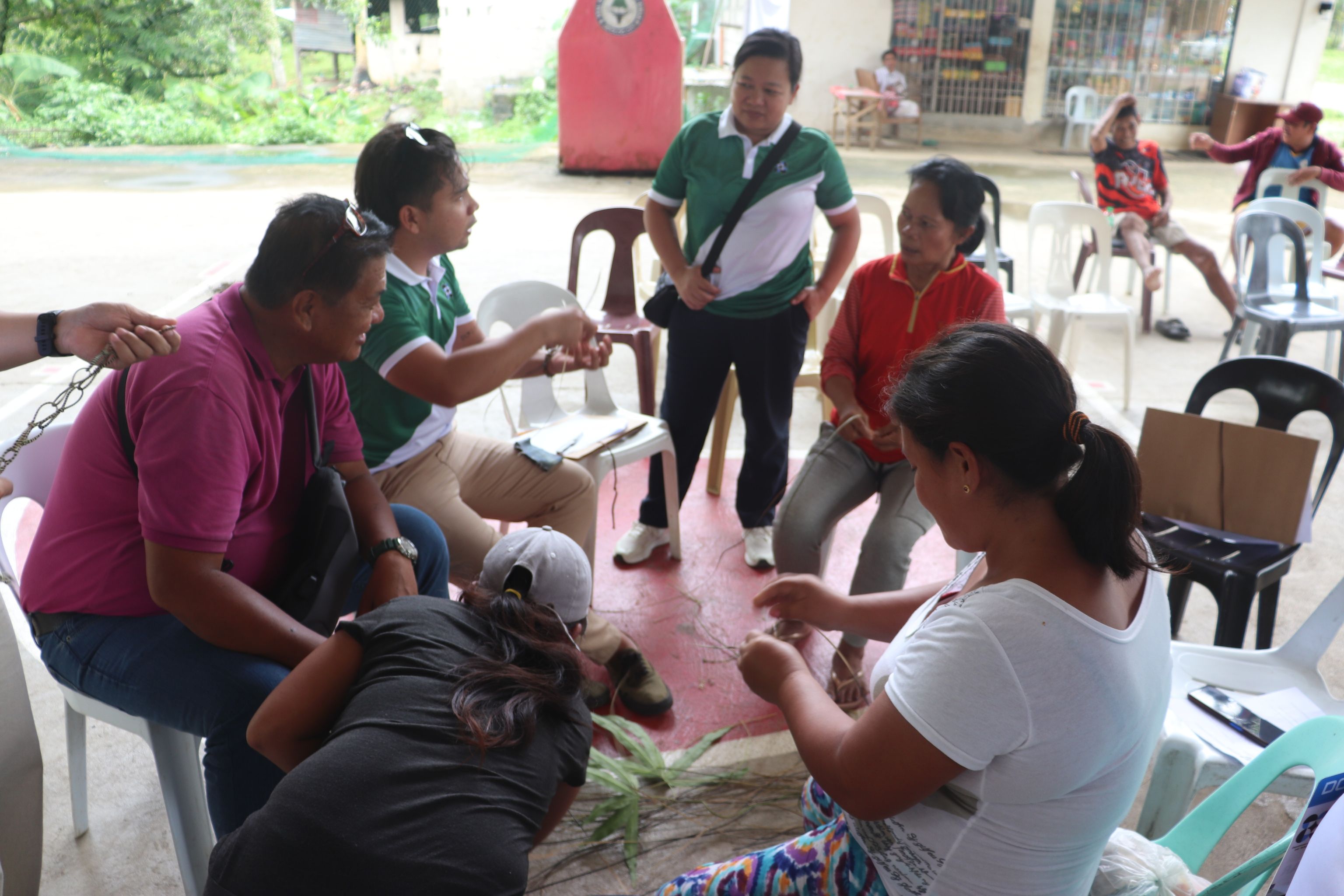
Because of their innovative way of utilizing the nito vine, they caught the attention of the Department of Science and Technology (DOST) who recently sent off a batch of their SalikLakbayers into the area.
Coined from two filipino words “saliksik” and “lakbay” meaning “research” and “journey” respectively, a SalikLakbayer is someone who goes to far flung areas in search of grassroots innovations, or more commonly known by its colloquial name diskartes.
Under the DOST’s Grassroots Innovation for Inclusive Development (GRIND) Program, their products were identified as a grassroot innovation (GI) under the endangered artisan and ethnobotanical categories which is when indigenous plants are used for food, livelihood, and medicine.
The DOST is currently trying to come up with interventions that will help improve their chances at gaining regular clients as well as ensuring the sustainability of the art now that the vines are slowly running out in their area.
In hopes of preserving the craft and all the cultural connotations that comes with it, Lillian said she is more than willing to teach the younger generation and anyone who is willing to learn.
As something so closely tied to our identity that nearly everyone who visits the country wants to bring it back as a souvenir, it is more than a business decision to keep the trade going but a cultural responsibility. (NBE/EDT/PJF/PIA9-Zamboanga del Norte)